PPR Cold and Hot Water Pipe Fitting Moulds: Meeting Industry Needs with Innovative Solutions
2025-07-10
PPR Cold and Hot Water Pipe Fitting Moulds: Addressing Market Demands
Introduction to PPR Moulds and Their Significance in the Industry
In the ever-evolving landscape of manufacturing and engineering, **PPR (Polypropylene Random Copolymer)** moulds for cold and hot water pipe fittings play a crucial role. These moulds are pivotal in producing high-quality piping systems widely used in residential, commercial, and industrial applications. With the increasing demand for effective and efficient plumbing solutions, the need for advanced PPR mould technology has never been greater.
The Role of PPR Moulds in Water Delivery Systems
PPR pipes are celebrated for their excellent thermal resistance, corrosion resistance, and lightweight nature. These attributes make them ideal for both hot and cold water applications. The moulds used to create these pipes must uphold strict manufacturing standards to ensure the final products meet the rigorous demands of the market.
Understanding Market Trends in PPR Pipe Applications
The global shift towards sustainable and efficient plumbing systems has led to a surge in the production of PPR pipes. Industry trends indicate that **sustainability**, **cost-effectiveness**, and **durability** are at the forefront of consumer preferences. As a result, manufacturers are increasingly investing in innovative mould designs to meet these market demands.
1. The Growing Demand for Sustainability in Plumbing
As environmental concerns rise, the demand for eco-friendly materials in plumbing systems has become a priority. PPR pipes, being recyclable and reducing energy consumption during manufacturing, align perfectly with these sustainability goals.
2. Increased Focus on Cost-Effectiveness
Cost efficiency remains a significant factor for contractors and builders. PPR pipes offer a longer lifespan compared to traditional materials, thus reducing maintenance costs and providing a higher return on investment. The moulds used for these pipes must ensure high precision and minimal waste during production.
3. High Durability and Performance Standards
The durability of PPR pipes is essential for their application in various environments. Mould manufacturers are tasked with creating products that maintain the integrity and performance standards required for both hot and cold water applications.
The Manufacturing Process of PPR Cold and Hot Water Pipe Fitting Moulds
The creation of PPR moulds for pipe fittings is a complex process that integrates advanced technology and skilled craftsmanship. Understanding this process is vital for stakeholders in the manufacturing sector.
Step 1: Design and Prototyping
The first stage involves a detailed design and prototyping phase, where specifications are established based on market needs. Advanced software tools are utilized for **3D modeling** to visualize the mould design and ensure its feasibility before moving into production.
Step 2: Material Selection
Choosing the right materials is crucial for the mould's success. Commonly, high-quality steel or aluminum alloys are chosen due to their durability and ability to withstand high temperatures during the moulding process.
Step 3: Precision Machining
Once the design is finalized, precision machining takes place. Computer Numerical Control (CNC) machines are utilized to create mould components with high accuracy, ensuring that all dimensions adhere to strict industry standards.
Step 4: Mould Assembly and Testing
After machining, the mould components undergo assembly. Rigorous testing is conducted to ensure the mould performs as expected under various conditions. This phase is critical for identifying potential weaknesses and making necessary adjustments.
Technological Advancements in PPR Mould Manufacturing
The PPR mould manufacturing industry continually evolves due to advancements in technology. Staying abreast of these developments is essential for manufacturers aiming to maintain a competitive edge.
Integration of Automation and Robotics
Modern mould manufacturing increasingly incorporates automation and robotics. These technologies enhance productivity, reduce labor costs, and improve precision in the production process.
Utilization of Advanced Materials
The introduction of new materials designed for high-performance moulds allows for improved durability and heat resistance. These materials contribute to the longevity of the moulds, ultimately benefiting the end-user with superior pipe performance.
3D Printing in Mould Production
3D printing technology has revolutionized the way moulds are conceptualized and produced. Quick prototyping and the ability to create complex geometries lead to innovative designs that meet specific customer needs.
Market Challenges for PPR Mould Manufacturers
Despite the growth in demand for PPR moulds, manufacturers face several challenges that must be navigated effectively.
1. Competition and Pricing Pressures
As more companies enter the market, competition intensifies. Manufacturers must balance quality with cost-effectiveness to remain viable while still delivering high-quality products.
2. Technological Adaptation Costs
Investing in new technologies can be costly. Manufacturers must carefully evaluate the return on investment when considering upgrades to their machinery and processes.
3. Regulatory Compliance and Standards
The industry is heavily regulated, with strict guidelines for manufacturing processes and product quality. Ensuring compliance with these regulations can be a significant challenge, requiring ongoing training and audits.
Future Trends in PPR Cold and Hot Water Pipe Fitting Moulds
As we look ahead, several trends are anticipated to shape the future of PPR mould manufacturing.
1. Increased Demand for Customization
With the rising preference for tailor-made solutions, manufacturers will need to offer customization options in mould design to cater to specific customer requirements.
2. Emphasis on Smart Manufacturing
The future of mould manufacturing is likely to see an increased shift toward smart manufacturing practices, including the Internet of Things (IoT) for real-time monitoring and data analysis.
3. Continuous Innovation in Materials and Processes
Ongoing research and development will lead to innovations in materials that enhance the performance and sustainability of PPR pipes, pushing manufacturers to adapt continually.
Conclusion
In conclusion, the landscape of **PPR cold and hot water pipe fitting moulds** is evolving rapidly due to market demands for sustainability, cost-effectiveness, and durability. Understanding the manufacturing process, technological advancements, and market challenges is essential for manufacturers aiming to thrive in this competitive industry. By embracing innovation and adapting to trends, manufacturers can position themselves for success in the future of PPR mould manufacturing.
Frequently Asked Questions (FAQs)
1. What are PPR moulds used for?
PPR moulds are primarily used to manufacture fittings for cold and hot water pipes, ensuring efficient water delivery systems in various applications.
2. How do PPR pipes compare to traditional materials?
PPR pipes are lightweight, corrosion-resistant, and energy-efficient, offering advantages over traditional materials such as metal or PVC pipes.
3. What is the manufacturing process for PPR moulds?
The manufacturing process involves design and prototyping, material selection, precision machining, assembly, and rigorous testing.
4. What are the current trends affecting the PPR mould industry?
Key trends include a focus on sustainability, cost-effectiveness, customization, and the integration of advanced manufacturing technologies.
5. How can manufacturers address market challenges?
Manufacturers can navigate challenges by investing in technology, ensuring regulatory compliance, and focusing on quality to remain competitive in the market.
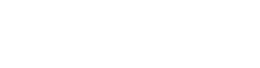
We provide exceptional products and quality services, ensuring that our products meet the relevant standards of various countries, and earning the trust and support of our customers.
CONTACT
103, Building 10, Lecheng Molding Industrial Park, Xinqian Street, Huangyan District, Taizhou city, Zhejiang Province