Understanding Plastic Valve Moulds: Key Insights for Professionals
2025-05-06
Plastic valve moulds play a crucial role in the manufacturing of various plastic components, particularly in industries that require precision-engineered parts, such as automotive, plumbing, and industrial applications. The process of creating these moulds involves a thorough understanding of materials, design, and manufacturing techniques, ensuring that the end products meet stringent quality standards.
The first step in creating a plastic valve mould is to design the mould itself. This involves using computer-aided design (CAD) software to create a detailed blueprint that outlines the specifications of the valve, including its dimensions, shape, and any necessary features such as channels or grooves. The design phase is critical, as it dictates the functionality and efficiency of the valve once produced.
After the design is finalized, the next step is the selection of materials for the mould. Common materials used include steel and aluminum, each offering different benefits. Steel is known for its durability and resistance to wear, making it suitable for high-volume production runs. On the other hand, aluminum is lighter and more cost-effective for smaller batches, providing flexibility for various projects. Understanding the strengths and weaknesses of these materials is essential for making an informed choice based on production needs.
Once the materials are chosen, the manufacturing process can begin. This typically involves machining the mould components with high-precision equipment to ensure they align perfectly. Following machining, the mould undergoes a finishing process, which includes polishing and heat treatment to enhance its performance and longevity. The accuracy achieved during this phase directly impacts the quality of the final plastic valve.
Injection moulding is the most common technique used to produce plastic valves. In this process, plastic pellets are heated until molten and then injected into the pre-made mould cavity. The material cools and solidifies, taking the shape of the mould. This method is favored for its efficiency and ability to produce complex shapes at scale.
Finally, the benefits of using plastic valve moulds are numerous. They not only allow for the production of lightweight and corrosion-resistant components but also enable the creation of intricate designs that might be difficult or impossible to achieve with traditional materials. Furthermore, the ability to mass-produce these components ensures that manufacturers can meet market demands effectively.
In conclusion, understanding plastic valve moulds is essential for professionals in the manufacturing processing machinery sector. By grasping the design, material selection, and production techniques involved, they can enhance their product offerings and remain competitive in an ever-evolving industry. As technology advances, so too will the methods of producing these critical components, making continuous learning and adaptation key to success.
The first step in creating a plastic valve mould is to design the mould itself. This involves using computer-aided design (CAD) software to create a detailed blueprint that outlines the specifications of the valve, including its dimensions, shape, and any necessary features such as channels or grooves. The design phase is critical, as it dictates the functionality and efficiency of the valve once produced.
After the design is finalized, the next step is the selection of materials for the mould. Common materials used include steel and aluminum, each offering different benefits. Steel is known for its durability and resistance to wear, making it suitable for high-volume production runs. On the other hand, aluminum is lighter and more cost-effective for smaller batches, providing flexibility for various projects. Understanding the strengths and weaknesses of these materials is essential for making an informed choice based on production needs.
Once the materials are chosen, the manufacturing process can begin. This typically involves machining the mould components with high-precision equipment to ensure they align perfectly. Following machining, the mould undergoes a finishing process, which includes polishing and heat treatment to enhance its performance and longevity. The accuracy achieved during this phase directly impacts the quality of the final plastic valve.
Injection moulding is the most common technique used to produce plastic valves. In this process, plastic pellets are heated until molten and then injected into the pre-made mould cavity. The material cools and solidifies, taking the shape of the mould. This method is favored for its efficiency and ability to produce complex shapes at scale.
Finally, the benefits of using plastic valve moulds are numerous. They not only allow for the production of lightweight and corrosion-resistant components but also enable the creation of intricate designs that might be difficult or impossible to achieve with traditional materials. Furthermore, the ability to mass-produce these components ensures that manufacturers can meet market demands effectively.
In conclusion, understanding plastic valve moulds is essential for professionals in the manufacturing processing machinery sector. By grasping the design, material selection, and production techniques involved, they can enhance their product offerings and remain competitive in an ever-evolving industry. As technology advances, so too will the methods of producing these critical components, making continuous learning and adaptation key to success.
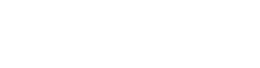
We provide exceptional products and quality services, ensuring that our products meet the relevant standards of various countries, and earning the trust and support of our customers.
CONTACT
103, Building 10, Lecheng Molding Industrial Park, Xinqian Street, Huangyan District, Taizhou city, Zhejiang Province