Wire conduit mold
Specialize in manufacturing all moulds of pipe fitting series: pvc drainage pipe fitting mould, ppr cold and hot water pipe fitting mould, PE pipe fitting mould...
Keywords:
Plasticpipe fittings moulds
Category:

Hotline:
Wire conduit mold
Detail
Solid wall tube mold:
Purpose: To produce solid pipes with uniform wall thickness and smooth inner and outer walls. Commonly used for building wire conduit, communication cable conduit, etc., requiring mechanical strength, flame retardancy, and insulation.
Mold features: The structure is relatively simple, with the core being the extrusion die head (mouth die and core rod), matched with a sizing sleeve and a cooling water tank. The key lies in precise control of wall thickness uniformity and outer diameter size. Mold design needs to consider material rheological properties, melt pressure distribution, and thermal expansion.
Bellows mold:
Purpose: To produce pipes with wavy inner and outer walls (single wall corrugated pipes, double wall corrugated pipes). The corrugated structure greatly improves the ring stiffness (resistance to external pressure) of the pipeline while maintaining flexibility and lightweight. Widely used in buried cable protection, optical cable protection, drainage and other fields.
Mold features: This is the most complex and representative series of wire conduit molds.
Modular molding module: The core is a series of metal modules (molding blocks) with specific corrugated grooves that move along the production line. These modules run in a loop on the track.
Extrusion die head:
Single wall corrugated tube: The die extrudes the tube blank, which is sucked into the groove of the forming module under vacuum adsorption, forming ripples. Accurate vacuum sizing and cooling control are required.
Double walled corrugated pipe: using co extrusion die head. The melt of the inner layer (smooth inner wall) and the outer layer (corrugated layer) is merged and extruded together in the die. The outer layer of molten material adheres to the forming module to form ripples, while the inner layer of molten material adheres to the inner sizing sleeve under internal air pressure or vacuum to form a smooth inner wall. The double wall corrugated pipe mold is one of the most technologically advanced and widely used wire conduit molds.
Cooling system: Bellows require an efficient cooling system to quickly shape complex corrugated shapes.
Special structure pipe mold:
Internal ribbed tube/spiral ribbed tube mold: produces pipes with spiral or axial reinforcing ribs on the inner wall to improve their compressive and flexibility capabilities. The design of the mold head requires machining corresponding rib groove channels on the core rod.
Open pipe/winding pipe mold: used for producing open pipes such as C-shaped and U-shaped that are easy to thread or spiral wound pipes. Special mouth mold design and cutting or winding devices are required for coordination.
Porous tube (bundle tube/honeycomb tube) mold: used to simultaneously extrude multiple small tubes (sub tubes) combined into a large tube. Adopting a multi-channel co extrusion die, the structure is complex, requiring consistent size and good bonding of each sub tube.
Key components of wire conduit series molds
Extrusion die head:
Mouth mold: forms the outer contour of the pipeline.
Core rod: forms the inner hole of a pipeline. Its design (such as straight section length, compression ratio, channel shape) is crucial for the uniformity of melt flow and product quality.
Mold body/bracket: supporting the core rod, with complex flow channels inside to evenly distribute the melt into the annular gap of the mouth mold. For co extrusion molds (such as double walled corrugated pipes), the mold structure is more complex and requires precise control of the convergence and interface bonding of each layer of melt.
Sizing system:
Vacuum sizing sleeve (box): the most commonly used. Using vacuum adsorption to make the molten tube tightly adhere to the inner wall of the sizing sleeve, accurately controlling the outer diameter size and roundness. It is extremely important for both solid wall pipes and corrugated pipes.
Internal pressure sizing: mainly used for solid wall pipes. Inject compressed air inside the tube blank to expand outward and tightly adhere to the inner wall of the sizing sleeve. Used for forming smooth inner wall layers in double walled corrugated pipes.
Design of sizing sleeve: Dimensional accuracy, surface smoothness, cooling water channel design, and vacuum/pore distribution directly affect the appearance, size, and performance of the pipeline.
Cooling system:
It usually includes multiple water tanks or spray boxes to gradually cool and solidify the pipes after sizing. Cooling efficiency and uniformity are crucial for preventing deformation, reducing internal stress, and improving production efficiency.
Tractor: Provides stable traction to pull the cooled pipes out of the production line at a constant speed.
Cutting machine/coiling machine: Cut or coil continuously produced pipes into coils according to a set length.
Forming module (specifically designed for corrugated pipes): A metal module that operates in a cyclic manner, and its groove shape determines the size and structure of the wave peaks and valleys of the corrugated pipe. The machining accuracy, fitting accuracy, and cooling efficiency of the module are key.
Considerations for choosing wire conduit series molds
Pipeline type: solid wall pipe? Single wall corrugated pipe? Double walled corrugated pipe? Internal rib tube? Decided the basic type of mold.
Pipeline specifications: outer diameter, inner diameter, wall thickness (or ring stiffness grade), length requirements.
Materials: PVC, HDPE, MDPE, PP, etc. Different materials have different melt characteristics, and the design of mold flow channels and temperature control need to be adjusted accordingly.
Production speed requirements: High speed production requires more precise molds, stronger cooling capacity, and more stable control systems.
Quality standards: dimensional tolerances, appearance requirements (smoothness, color uniformity), physical and mechanical performance requirements (ring stiffness, impact resistance, flat test, etc.).
Equipment matching: The mold must match the specifications of the existing extruder (screw diameter, output, connection method) and other equipment on the production line (traction, cutting, etc.).
Previous
Bellows module
Next
RELATED MOULDS
The main difficulty in achieving high precision with external thread direct molds
The main difficulty in achieving high precision with external thread direct molds
Difficulty in Precision Control of Sixteen Thread Cap
The main reason for the difficulty in demolding caused by spherical molds
The main reason for the difficulty in demolding caused by spherical molds
MESSAGES
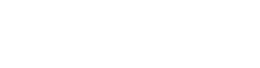
We provide exceptional products and quality services, ensuring that our products meet the relevant standards of various countries, and earning the trust and support of our customers.
CONTACT
103, Building 10, Lecheng Molding Industrial Park, Xinqian Street, Huangyan District, Taizhou city, Zhejiang Province