The main reason for the difficulty in demolding caused by spherical molds
Specialize in manufacturing all moulds of pipe fitting series: pvc drainage pipe fitting mould, ppr cold and hot water pipe fitting mould, PE pipe fitting mould...
Keywords:
Plasticpipe fittings moulds
Category:

Hotline:
The main reason for the difficulty in demolding caused by spherical molds
Detail
Geometric shape (without draft angle):
A sphere is a perfect convex surface, and the distance from the geometric center to any point on the surface is equal.
This shape has no draft angle at all. The draft angle refers to the slight inclination angle (usually a few degrees) of the mold wall designed to make it easier for the formed object to slide out of the mold.
During the demolding process, the molded product needs to be evenly and simultaneously separated from the entire inner surface of the mold. Any local adhesion or friction will hinder the entire demolding process.
Large contact area:
Compared to a simple cube or cylinder, the contact area between the spherical shaped product and the inner surface of the mold is relatively larger and more continuous. This means that the total amount of frictional force that needs to be overcome is greater.
The 'vacuum' effect:
When the sphere is tightly adhered to the smooth inner wall of the mold, attempting to pull it out may create a local vacuum or negative pressure area between the sphere and the mold. This will generate additional suction and resist demolding forces, especially when the material is soft (such as silicone, chocolate, gummies) or the mold surface is very smooth.
Material shrinkage and adhesion:
Shrinkage rate: All materials will shrink during curing or cooling. If the shrinkage rate of the material is low or the shrinkage direction is uneven (although the sphere shrinks relatively uniformly, the properties of the material itself may cause local differences), it may not naturally detach from the mold wall, but instead "tighten" the mold.
Adhesion: There may be strong adhesion between certain materials (such as certain resins, silicone, and insufficiently demolded chocolate) and mold materials (especially certain plastics or metals), which exacerbates the difficulty of demolding.
Variables affecting the difficulty of demolding
Mold material:
Flexible molds (such as food grade silicone): This is the easiest ball mold to demold. Silicone has excellent flexibility, allowing you to break the vacuum effect by squeezing, stretching, and twisting the mold, and gradually "squeeze" the sphere out. This is the most commonly used method for making spherical chocolates, mousse, ice hockey, and more.
Hard molds (such as metal, hard plastic, resin): demolding is the most difficult. Unable to assist in demolding by deforming the mold. It is necessary to strictly rely on the draft angle (without the sphere), ejection mechanism, strong release agent, and the shrinkage characteristics of the material itself. Plastic balls or metal castings commonly used in industrial injection molding.
Mold structure:
Split line design: Hard ball molds are usually composed of two halves or multiple lobes. When demolding, first open the mold shell, and then remove the spheres from the two halves of the mold cavity separately. This is much easier than a one-piece spherical cavity, as each hemispherical cavity itself has a certain draft angle (from the parting line to the center). A well-designed parting line position and matching accuracy are crucial.
Top out mechanism: In industrial injection molds, a top pin or top plate is designed inside the mold cavity to use mechanical force to push the sphere out of the mold cavity after opening. This is necessary for demolding hard molds.
Exhaust design: Good exhaust helps to avoid vacuum effects.
Molding material:
Shrinkage rate: Materials with high shrinkage rates, such as many plastics and resins, significantly reduce in size after curing and cooling, making them easier to naturally detach from the mold wall.
Elasticity/Softness: Soft and elastic materials (such as rubber, silicone, gummies, and freshly solidified chocolate) are easier to detach from complex shapes than hard and brittle materials because they can withstand certain deformations.
Surface tension/viscosity: Viscous or high surface tension materials (such as certain resins, honey) are more likely to adhere to molds.
Surface treatment and release agent:
Mold surface smoothness: An extremely smooth surface can sometimes increase the risk of vacuum adsorption, but a rough surface can increase friction and demolding resistance. Usually requires appropriate polishing.
Release agent: crucial! Whether it is hard mold or soft mold, the use of appropriate release agents (such as food grade oil, powder spray; industrial release wax, release spray) can significantly reduce the adhesion and friction between materials and mold, which is the key step for successful demoulding.
Size:
The larger the size of the sphere, the larger the contact area, and the more obvious the vacuum effect may be, requiring a greater demolding force.
Summarize the difficulty level of demolding
The easiest: using flexible silicone molds+cooperating with extrusion/stretching operations+using release agents. (Commonly used in home baking, candy making, and handmade resin)
Medium difficulty: Hard two-piece mold+high shrinkage/elastic material+strong release agent. (Commonly seen in industrial injection molding of small plastic balls and casting)
Most difficult: integrated hard ball mold cavity+low shrinkage rate/hard brittle material+no effective release agent/ejection mechanism. (Rarely seen in practice, as it is almost impossible to demold)
How to improve the demolding of spherical molds
Preferred silicone mold: For DIY, food, and small products, silicone molds are the best choice.
Be sure to use release agent: choose and use release agent correctly according to the material and mold type. Apply evenly and in moderation.
Fully cured/cooled: Ensure that the material is completely cured or cooled to achieve sufficient strength and dimensional stability.
Flexible mold operation technique: Gently knead and stretch the edge of the mold, and slowly push it out from the bottom or side of the sphere. Avoid poking the finished product directly with sharp objects.
Key points of hard mold design:
It is necessary to use a split structure (usually two halves).
Design a reasonable ejector system (ejector pin, push plate).
Optimize the position of the parting line and machining accuracy.
Polish the surface of the mold cavity appropriately.
Choose materials with high shrinkage rate.
Consider material properties: If possible, choose materials with high shrinkage or some elasticity
Conclusion: Demolding spherical molds is indeed more challenging than shapes with draft angles, especially when using hard molds. However, by selecting suitable mold materials (especially flexible silicone), carefully designing mold structures (for hard molds), strictly using appropriate release agents, and mastering correct operating techniques, the difficulty of demolding can be significantly reduced and perfect spherical products can be successfully obtained.
Previous
Next
Previous
REDUING BUSH
Next
RELATED MOULDS
The main reason for the difficulty in demolding caused by spherical molds
The main reason for the difficulty in demolding caused by spherical molds
MESSAGES
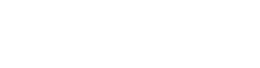
We provide exceptional products and quality services, ensuring that our products meet the relevant standards of various countries, and earning the trust and support of our customers.
CONTACT
103, Building 10, Lecheng Molding Industrial Park, Xinqian Street, Huangyan District, Taizhou city, Zhejiang Province